É cada vez mais frequente a utilização de controles remotos em garagens, pois o preço geralmente compensa o desconforto de ter que abrir os portões em dias de chuva, além de economizarem o nosso tempo. Só que, com o uso constante, volta e meia estes controles começam a falhar.
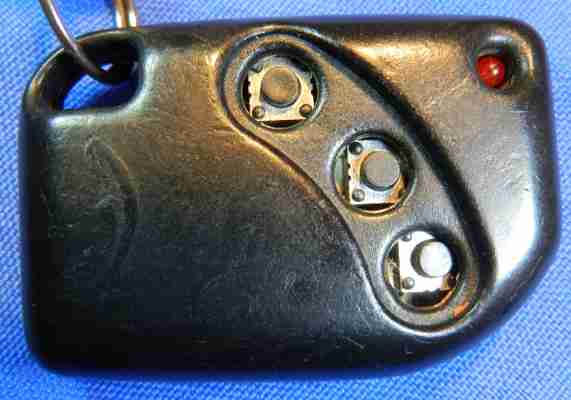
Neste post, mostro algumas dicas de conserto, que poderão evitar de jogá-los precocemente no lixo. Inclusive recuperá-los, caso tenham submergido em algum líquido ou tenham vazado a pilha. Também comento os componentes utilizados na construção destes sistemas.
O controle remoto, um transmissor de RF
Primeiramente, é importante comentar sobre o modo de trabalho destes dispositivos, pois isto poderá evitar a utilização indevida, que costuma causar frequentes defeitos.
O controle é um pequeno transmissor de radiofrequência (RF), de baixíssima potência (figura 1). Ele gera um sinal codificado, que modula as ondas de RF, que geralmente estão na casa das centenas de Mhz.
Atualmente (2013), as frequências utilizadas pelos controles remotos são 280, 292, 299, 315 e 433 Mhz. As duas últimas são mais comuns. Estas frequências ficam entre os canais 13 e 14 de televisão.
Os canais de TV de 2 até 13 estão dentro da faixa de VHF (Very High Frequency), que vai de 30 a 300 Mhz. O canal 13 vai até 216 Mhz. Já o canal 14, pertence à faixa de UHF (Ultra High Frequency) e começa em 470 Mhz. A faixa de UHF começa em 300 Mhz.
Há, então, um intervalo que pertence a ambas as faixas (VHF e UHF), que fica entre 216 e 470 Mhz. Esta banda de frequências é utilizada para serviços diversos, conforme informação do sítio do professor Wilians Cerozzi Balan [1], que tem ótimas matérias na área de produção de programas para TV. Na ibytes [2], outra página muito interessante, de Pedro Gercino Til, está escrito que nesta faixa de frequências não é permitida, pela legislação, a divulgação de uso.
Tentei saber mais sobre as atribuições desta faixa (216 a 470 Mhz) na Anatel, mas a página da agência não ajudou muito. As informações são um tanto dispersas, com poucas explicações. Ainda assim, lá encontrei o Plano de Atribuição, Destinação e Distribuição das Faixas de Frequências no Brasil, versão 2011, com 178 páginas [3]. Neste plano, pode-se ver que a faixa de 216 a 470 MHz é utilizada em diversas áreas, mas a destinação não ficou muito clara, há a necessidade de esclarecer alguns termos técnicos.
Também na página da Anatel, pode-se acessar o Quadro de Distribuição de Frequências no Brasil [4], que dá um bom panorama do uso da faixa de RF.
O funcionamento do controle
Quando o usuário aperta um botão do controle remoto, a pilha interna deve energizar o circuito e começar a transmitir um código, diversas vezes por segundo. Enquanto a pessoa mantiver o botão pressionado, os códigos serão transmitidos. Mas há um pequeno tempo inicial até a estabilização do sinal, em que poderá não haver nenhuma transmissão.
Cada código é composto por um trem de pulsos específico, separado por um intervalo sem sinal, para permitir o reconhecimento do seu início e fim pelo receptor. Os pulsos devem ter potência suficiente para atingir o estágio de recepção e controle, que fica junto ao motor do portão.
O receptor é como um rádio, que escuta as ondas de RF que chegam até sua antena. Ele deve captar estes débeis sinais transmitidos pelo controle remoto, amplificá-los, selecioná-los, convertê-los em códigos digitais e compará-los com o código armazenado na sua memória. Só quando o código for reconhecido como apto é que o motor do portão será acionado.
Este processo pode demorar certo tempo (alguns segundos), dependendo da intensidade da poluição eletromagnética existente no local – também conhecida por electrosmog, ver referências [5], [6], [7] e [8] -, da quantidade de superfícies que irão refletir/atenuar o sinal, da qualidade das antenas de transmissão e recepção e da seletividade do receptor, dentre outros motivos.
Pode-se ter uma ideia de como é esta transmissão de pulsos na figura 2, que mostra uma captura de sinais de 433 Mhz [9], gerados pelo circuito integrado PT2262, que faz par com o receptor PT2272. A imagem mostra 4 sequências de pulsos, cada uma delas formando um código completo. Além disso, pode-se notar a deformação dos pulsos, que no controle, ao chegar ao estágio transmissor, ainda tinham formas perfeitamente definidas, pois são provenientes de circuito digital.
Vários fatores, como instabilidade da tensão de alimentação do transmissor, ou reflexões e interferências sobre o sinal, que constituem o ambiente de transmissão e recepção, poderão afetar a qualidade do sinal, em maior ou menor intensidade. Olhando com mais cuidado a figura 2, é possível notar que as sequências de pulsos são diferentes entre si, principalmente no começo de cada código. Isto pode ter sido causado por alguma situação aleatória, não controlada, no teste.
A respeito de radiofrequência, é importante saber que objetos maiores do que o comprimento de onda do sinal, irão refleti-lo. Por exemplo, a frequência de 433 Mhz tem um comprimento de onda aproximado de 70cm. Qualquer objeto maior que isso refletirá sinais desta frequência. Especialmente se for metálico. Para maiores informações sobre antenas e a propagação das ondas eletromagnéticas, consultar as referências [10], [11] e [12].
Percebe-se, assim, que o trabalho do receptor é espantoso, pois consegue discernir e reconhecer o sinal destinado a ele, apesar de todas as dificuldades e interferências.
A segurança
Bem no começo dos controles automatizados de portões, era realizada apenas a transmissão de alguma frequência de RF, que ao ser identificada pelo receptor, acionava o motor. Não havia qualquer tipo de codificação, até porque existiam bem poucos aparelhos deste tipo e a fabricação era mais artesanal. Com o aumento da quantidade destes equipamentos e da preocupação com a segurança, apareceram os primeiros sistemas comerciais de codificação, muitos deles ainda hoje utilizados.
Estes circuitos integrados dedicados dispunham de um conjunto de conexões (pontes de ligação ou jumpers) que ficavam ligadas ou não, formando uma combinação, que para ser reconhecida, deveria ser igual à do receptor. A United Microelectronics (UMC) tinha o UM3750 [13], equivalente ao UM86409 e ao MM53200, este da National [14]. O mesmo circuito integrado era utilizado tanto na codificação (para a transmissão), quanto para decodificação (na recepção). Foram muito utilizados na Europa.
Por aqui, os circuitos integrados da Holtek, da linha HT12E (codificador) e HT12D (decodificador) [15], são um exemplo famoso deste tipo de codificação. Há também outros fabricantes, como Princeton [16], com o par PT2262 e PT2272; Freescale [17], com os MC145026P e MC145027P e Rentron [18], com o conjunto CIP-8E e CIP-8D.
O número de combinações varia conforme o modelo do circuito integrado. Por exemplo, os da UMC, National e Holtek citados acima permitem 4096 combinações. Isto ocorre porque as conexões da codificação aceitam dois estados somente (ligado ao terra ou desligado).
Já os integrados da Princeton e Freescale, por utilizarem pinos tristate, permitem mais de 530 mil combinações. Os pinos tristate podem ser ligados ao terra, ao positivo ou ficar sem ligação.
Mas este tipo de configuração tem uma fragilidade importante. Se um dos usuários perder o controle remoto, todos os que utilizam aquele portão deverão trocar a codificação conjuntamente, pois o receptor só reconhece um código. Ou seja, todos os controles remotos em uso para aquele portão, deverão ser alterados por um técnico.
Assim, a imensa variedade de combinações não valerá muito, se faltar um cuidadoso controle dos códigos já utilizados. A falta de exclusividade para o código definido nos jumpers poderá tornar-se um sério problema.
O grande número de fabricantes de circuitos de automação, inclusive os de fundo de quintal, além da necessidade eventual de alteração da combinação por técnicos isolados, aumenta muito a possibilidade da coincidência de códigos entre controles diferentes.
Se um controle utilizar uma frequência de transmissão semelhante a de outro portão eletrônico e tiver a mesma combinação, muito provavelmente o circuito poderá acioná-lo também. É um prato cheio para meliantes. Quando conseguem um controle, saem pela cidade apertando os botões. E às vezes, ocorre um “Abre-te, sésamo!”…
Sistemas mais modernos diminuíram este problema, pois são baseados em um código único, gerado por cada controle, que é cadastrado no receptor.
Tal código é gravado no circuito integrado pelo fabricante do controle remoto. A tecnologia OTP (One Time Programmable) garante que o componente possa ser gravado somente uma vez. Ou seja, cada controle remoto sai da fábrica pronto, com uma combinação exclusiva, que não poderá ser refeita.
A linha HT6P20x, da Holtek[19], é um exemplo disto, e permite mais de 16 milhões de combinações. Se alguém perder um controle remoto deste tipo, é só descadastrá-lo no receptor, ou limpar a memória e recadastrar somente os que devem ficar ativos.
A segurança melhorou, mas ainda assim os fabricantes de controles remotos estão livres para utilizarem o código que quiserem. Talvez fosse melhor que as combinações já viessem dos fabricantes dos chips, com a garantia da inexistência de outro componente idêntico, mas no momento (2013) não sei se já existe algum componente deste tipo.
E para deixar de cabelo em pé aqueles que estão preocupados com segurança, na internet já podem ser encontrados, por menos de 30 reais (em 2013), controles remotos copiadores, que clonam um controle, desobrigando o cadastramento na memória do receptor. É a velha briga do gato e do rato…
Um esclarecimento: os fabricantes aqui citados foram os que aparecem nos circuitos integrados dos controles remotos com os quais tive contato. Por isto, certamente haverá muitos outros fabricantes de chips, que não citei por não conhecê-los. Inclusive, mesmo as marcas citadas tem diversos outros modelos de circuitos integrados para controle remoto, para as mais diversas finalidades.
Caso alguém queira conhecer mais a fundo estes interessantes componentes, nas referências [13] a [19] estão reunidos os datasheets. Há diversos artigos práticos a partir da referência [20] até [29], como o FT-151, um transmissor de controle remoto, de longa distância (400mW). Há também experimentos com microcontroladores e com transmissão de mais de um canal de codificação.
O Acionamento
O modo mais eficaz para acionar o sistema é pressionar o botão do controle remoto de 1 a 3 segundos, para dar tempo dele transmitir adequadamente diversos trens de pulsos, facilitando o trabalho do receptor. Daí, aguardar alguns instantes e, caso o portão não tenha sido acionado, pressionar novamente o botão do controle, do mesmo modo já descrito. Com a prática, o usuário perceberá o tempo correto.
O que deve ser evitado é o acionamento rápido do botão do controle, repetidas vezes (vários e insistentes click’s). Dependendo da arquitetura interna do controle remoto, isto poderá gerar códigos incompletos ou muito deformados, contribuindo somente para aumentar a poluição eletromagnética.
Além disso, muitos circuitos de receptores, ao receberem sinais truncados ou muito diferentes do esperado, disparam um retardo e não analisam mais nada por algum tempo, obrigando o apressado usuário a esperar mais ainda.
Daí, pensando que o controle não funciona direito, ele aperta firmemente a tecla e, na esperança de que o alcance aumente com a força, quase esmaga o coitado do aparelhinho…
Os Defeitos
Os receptores, em geral, danificam-se pouco, pois aceitam bem as variadas condições de uso. Eventualmente, podem travar um dos relés de acionamento do motor, o que pode ser evitado com um pequeno circuito adicional, comentado em post anterior (acesse ele AQUI).
Já os transmissores (controles remotos), apresentam problemas seguidamente. Um deles, fica por conta da pressão excessiva exercida sobre as teclas. Com isso, as chaves internas danificam-se, tornando os acionamentos aleatórios ou até impossíveis. Estas chaves são interruptores de contato momentâneo, chamadas de “tact”. Geralmente são quadradas, tendo 6 mm de lado.
Este problema pode ser resolvido trocando estas chaves por outras de boa qualidade, como as da Omron, da linha B3F (em nosso caso) – ver figura 3 e referência [30]. Ou, caso uma das chaves não seja utilizada, trocá-las entre si.
Há também controles com teclas de borracha, que invariavelmente dão problemas, devido ao suor dos dedos: ou elas amolecem e ficam pegajosas, ou endurecem e começam a quebrar em pedacinhos. Ou as duas coisas, nesta sequência. Melhor escolher controles de teclas plásticas, ou que sejam de silicone. O problema é diferenciar o silicone da borracha comum…
Eu tive um controle que perdeu toda a borracha das teclas, e utilizei ele assim por vários anos, sem problemas. As chaves pararam de dar defeito, pois quando ficaram expostas, permitiram sentir exatamente qual a pressão necessária para acioná-las, sem precisar espremê-las – ver a figura 4. Como efeito colateral, o controle ficou com aversão à água…
Apesar das chaves causarem problemas, talvez as falhas mais comuns sejam as ditas “soldas frias”. É um antigo termo de eletrônica, do tempo das válvulas. Na época, muitos soldavam uma conexão e logo a assopravam, para esfriá-la. Isto evitava que queimassem os dedos, pois estavam segurando os fios e peças.
Só que, ao assoprar, o incauto solidificava somente o exterior da gota de solda. Daí, ele soltava a conexão e ela movimentava-se, enquanto o restante da solda endurecia. Noutras vezes, o soldador tinha potência insuficiente e não aquecia bem toda a área de soldagem, piorando a situação.
Por causa destes descuidos, resultava que a gota de solda ficava fosca, com aparência de pedra, com diversos pedacinhos soltos, o que causava frequentes falhas. Hoje em dia, o termo solda fria caracteriza qualquer ponto de solda que está falhando.
As placas de circuito impresso dos controles remotos normalmente passam por um processo de soldagem automatizado, no qual a quantidade de solda aplicada é reduzida ao mínimo. Se não houver correção manual de alguns pontos de solda, poderão aparecer facilmente locais de soldas frias, principalmente naqueles sujeitos a esforços mecânicos.
Outra causa de defeitos, mais recente, é motivada pelo uso da solda sem chumbo (que obedece a norma RoHS – ver referências [31] e [32]), que é pouco maleável e sempre fica com a aparência fosca. A característica quebradiça, além do ponto de fusão mais alto, fazem desta nova solda um transtorno para qualquer técnico de eletrônica.
Os pontos mais corriqueiros das falhas de solda são os contatos da pilha. Por causa do peso dela e da necessidade de pressão constante sobre suas extremidades, as chapinhas metálicas que realizam esta função são bastante exigidas e tendem a danificar os pontos de solda, como se pode ver na figura 5.
Este problema poderia ser minimizado caso os fabricantes decidissem projetar melhor o ancoramento destas chapas à placa de circuito impresso. Além disso, muitas indústrias não fazem estas chapas com aço inox ou outra liga metálica que tenha uma boa resiliência – que é a capacidade do metal de voltar à posição/forma original após a deformação, algo como o efeito de uma mola.
Às vezes, é necessário corrigir a forma destas peças de contato, pois são tão moles que a pilha acomoda-se no lugar, criando uma pequena folga, em vez de ficar sob pressão constante. Certamente haverá problemas de funcionamento, pois a alimentação do circuito estará sujeita a maus contatos.
Outra falha, mais difícil de notar, é no led do controle. Muitas vezes, este componente não é somente um indicador e faz parte do circuito de acionamento do transmissor. Se ele está estragado e não liga, o controle não funciona. O integrado da Princeton, o PT2262, por exemplo, aciona o estágio de RF através do led, conforme sua folha de dados [16].
Como o led tem uma janela que dá para o ambiente externo ao invólucro, ele fica sujeito a esforços e poderá danificar sua solda, como se vê na figura 6.
As chaves também podem apresentar solda fria, neste caso dispensando sua troca. Inclusive, o modo mais adequado para iniciar um conserto destes dispositivos é conseguir uma lupa de grande aumento e uma luz forte. Com eles, pode-se pesquisar os defeitos na placa com mais tranquilidade.
A solução dos problemas com as soldas é uma adequada ressoldagem. Para que este trabalho seja duradouro, é necessário limpar totalmente as áreas expostas à solda. O ideal é desmontar a peça, estanhá-la em separado, limpar a placa, retirando toda a solda antiga, e só então ressoldar.
A figura 7 mostra que a peça metálica que liga um dos pólos da pilha não estava com a camada de solda bem espalhada. Percebe-se a falta de estanhamento em parte da superfície dos dois pinos que ancoram (por soldagem) a peça à placa, o que facilitou o mau contato.
Na figura 8, aparece a placa estanhada adequadamente e na figura 9, a peça remontada. Durante a remontagem, é interessante encontrar um modo de apoiar e firmar a placa com os componentes e a peça metálica, de maneira que as mãos fiquem livres para manusear a solda e o ferro de soldar. Muitas vezes, a falta de alinhamento da peça metálica irá forçar a trilha de cobre da placa de circuito impresso, o que levará a novos e piores defeitos.
Em alguns controles, pode-se utilizar uma das faces do próprio invólucro como gabarito, deixando a camada de solda acessível e possibilitando o alinhamento correto do contato da pilha. Mas é necessário cuidar para que o tempo de soldagem não faça derreter o plástico que apoia as peças.
Já me ocorreu também de led’s trincarem internamente, o que os deixa inúteis. Por causa dos terminais muito curtos, qualquer esforço sobre o componente poderá danificá-lo. Veja, por exemplo, o led da figura 10, que está torto por causa da pressão mecânica a que foi submetido.
Para confirmar sua condição funcional, é preciso retirá-lo da placa e testá-lo na escala de diodo do multímetro, que apresentará uma queda de tensão de 1,8V, aproximadamente. Verificar também se os terminais estão firmes.
Se o led estiver bom e for recolocado na placa, é necessário que a ressoldagem seja feita rapidamente, pois o calor intenso também poderá queimá-lo, já que os terminais são muito pequenos e não fornecem área suficiente para dissipação do calor (ver figura 11).
A pilha vazou
Outro problema comum é o vazamento da pilha de 12V. O calor excessivo é a principal causa de vazamento de qualquer pilha. Falo isto por experiência própria. Deve-se evitar sempre a exposição direta à luz do sol de qualquer equipamento alimentado a pilhas.
Uma tarde de sol de verão sobre um controle remoto é suficiente para iniciar um processo de vazamento. Nestas condições e dentro de um carro, que pode alcançar 70 °C, é garantido que irá vazar. Na figura 12 pode-se notar que a pilha já está corroída e o respectivo contato no controle começou a escurecer.
Caso tenha ocorrido vazamento, a possibilidade de oxidação dos contatos aumenta radicalmente com o tempo. Por isto, é necessário revisar constantemente o controle para evitar este problema. Principalmente quando se nota que o alcance de acionamento está diminuindo.
Confirmado o vazamento, a pilha do aparelho deve ser descartada na primeira oportunidade. Também é preciso remover qualquer vestígio de corrosão, raspando o óxido das partes metálicas, se houver, e lavando a placa com benzina ou álcool isopropílico. Depois, pode-se aplicar uma leve camada de graxa clara nos contatos da pilha e no seu entorno. A figura 13 mostra a pilha e a placa de contato já com uma camada de graxa de silicone. Geralmente o pólo negativo é o mais prejudicado.
Como a graxa veda as superfícies ao ar, a oxidação é minimizada e até eliminada. Porque a oxidação é uma reação química que tem o oxigênio como elemento ativo, daí o nome. Impedindo o contato do metal com o oxigênio, a oxidação fica dificultada.
Óleos desengripantes, como o WD-40, são muito finos e penetrantes e podem escorrer para fora do controle, com o calor. Apesar disso, podem ser utilizados como hidrorrepelentes, como forma de prevenção contra o ataque de líquidos sobre a placa. Na referência [33] há um link para um artigo sobre os diversos usos do WD-40.
Controles mais modernos utilizam pilhas de lítio de 3V, que não tem o hábito de vazar, só que podem inchar ou oxidar levemente a borda (figura 14). Caso isto ocorra, será melhor trocar a pilha, mesmo que sua tensão esteja normal. A área de contato na placa também poderá ter sido danificada.
Atualmente, não conheço pilha que não vaze. Se a temperatura ambiente for alta, até o simples efeito galvânico dos metais encostados à pilha, somado aos gases emitidos por ela, à umidade ambiente e ao suor dos dedos, este último resultante de manipulação dos componentes internos do controle, poderá desencadear a corrosão.
Se o circuito impresso foi atingido, a recuperação será trabalhosa, talvez impossível. Para evitar que a corrosão seja irreversível, pode ser interessante fazer um cronograma de troca das pilhas dos controles, por exemplo uma vez a cada ano. Ou, no mínimo, uma revisão a cada trimestre. Conforme a exposição ao calor, a troca poderá ser abreviada.
A cada revisão convém testar o valor da tensão da pilha, pois se estiver muito baixa, o funcionamento do controle será prejudicado. Para realizar o teste, a figura 15 mostra um modo de fazê-lo, com a pilha no lugar e as pontas de prova nos terminais na placa de circuito impresso. Medir o valor de tensão da pilha, depois acionar algum dos botões do controle e medir novamente, para identificar a diferença de tensão quando há carga (figura 16).
O teste mostrado aqui foi feito com 3 pilhas, duas delas em uso e uma retirada da cartela naquele momento. O controle remoto consumiu energia suficiente para baixar, com carga (led ligado) 1,77 %, 1,85 % e 14,32 % da tensão em aberto. O consumo do controle, quando ativado, foi de 1,9 mA. Se o acionamento do controle baixar a tensão da pilha em mais de 20% do seu valor nominal, ela já estará com pouca vida útil, pois o alcance diminui bastante.
O controle caiu na água
Tanto faz se o controle caiu na água do mar, da piscina ou da máquina de lavar roupas, o mais importante é abri-lo imediatamente, separando a placa de circuito impresso.
Esta técnica, utilizei muito para o conserto de televisores, e ajuda bastante quando há corrosão. Para preparar o tratamento “de choque”, colocar água para ferver, 1 a 2 litros.
Segurar com uma pinça ou alicate a placa inclinada e deitar água fervente sobre toda a superfície, tanto no lado da solda, quanto no dos componentes. Apesar destas placas ficarem expostas, na fábrica, por poucos segundos, a temperaturas de mais de 200° C no processo de soldagem, a água somente atinge 100° C.
Mesmo assim, é melhor evitar que o líquido toque peças plásticas, como as chaves, pois poderão deformar. Outro cuidado é o trimmer, um capacitor variável que ajusta a frequência de transmissão e geralmente está coberto por parafina. Se a água quente cair em cima, a parafina derreterá.
Levar a placa imediatamente ao sol, de modo a aproveitar o calor da água e somá-lo à radiação solar, apressando a secagem.
As outras partes, lavar normalmente com água corrente e um pouco de sabão comum, suficiente para fazer espuma. Se tiver um pincel pequeno, ajuda muito para limpar sujeiras incrustradas. Enxaguar bem e também levar ao sol.
A pilha, por ter na sua composição componentes porosos, não pode ser lavada com água e sabão. O ideal é limpá-la com papel e álcool, cuidando principalmente das extremidades. Evitar expô-la ao calor.
Nas emergências, como na praia, se não houver água quente, poderá ser utilizada água corrente.
Deixar tudo secar, por meia hora, no mínimo. Ou utilizar um secador, meio de longe. Na falta de sol e secador, utilizar papel higiênico seco, cuidando para não deixar fiapos espalhados pela placa, que com a umidade poderiam levar a outros defeitos. Com todas as peças bem enxutas, o controle pode ser remontado.
Porque utilizar mais água?
Foi utilizada água quente porque o importante, para o defeito do tópico anterior, é diluir e retirar os sais da placa, já que a água do mar é altamente condutora de eletricidade. Água com detergente ou com altos níveis de cloro também conduz eletricidade e pode oxidar severamente o circuito. Com a diminuição da quantidade de sais e outros compostos químicos sobre a placa, o controle poderá voltar a funcionar.
Ainda assim, a longo prazo, as chaves poderão falhar, pois geralmente não são à prova d’água. O seu interior pode ter sido contaminado, o que torna possível a oxidação dos contatos.
E quando o controle é montado com peças minúsculas, como as do tipo SMD (Surface Mounting Device, ou Dispositivo de Montagem em Superfície), ocorre outro problema. A tecnologia SMD não utiliza furos na placa para os componentes, pois todos eles são soldados no lado das trilhas de cobre.
Neste caso, poderão haver espaços tão pequenos e escondidos que não será possível limpá-los, facilitando a corrosão de longo prazo e as futuras fugas de corrente entre os terminais. Isto é uma realizade em telefones celulares, onde a miniaturização é absurda. Se um destes aparelhos cai na água, dificilmente consegue ser recuperado.
Para exemplificar, na figura 17 aparecem 3 capacitores SMD de um controle remoto. Por baixo deles, passam duas trilhas de cobre. Cada capacitor tem aproximadamente 3 mm de comprimento por 2mm de largura…
Na montagem destes capacitores, foi utilizada uma grande quantidade de adesivo (gotas de cor creme), que dificulta a corrosão por debaixo dos componentes. Mas nem todos os fabricantes fazem isso. Às vezes, o tamanho menor pode ser uma desvantagem…
Por outro lado, se os controles remotos fossem todos herméticos, o contato destes aparelhos com a água não causaria danos. Claro, toda melhoria tem seu custo inerente, e por serem controles baratos, os fabricantes não se preocupam muito com isto.
Referências
[1] Wilians Cerozzi Balan – Distribuição do espectro de frequências – http://www.willians.pro.br/frequencia/cap3_espectro.htm
[2] ibytes – página de Pedro Gercino Til (ou Piava Branca) – Espectro eletromagnético – http://www.ibytes.com.br/tabela-das-frequencias-utilizadas-e-seus-respectivos-servicos/
[3] Anatel – Plano de Atribuição, Destinação e Distribuição das Faixas de Frequências no Brasil – Versão 2011 – http://www.anatel.gov.br/Portal/exibirPortalRedireciona.do?codigoDocumento=268709
[4] Anatel – Quadro de Distribuição de Frequências no Brasil – http://www.anatel.gov.br/Portal/exibirPortalRedireciona.do?codigoDocumento=98580&caminhoRel=In%EDcio-Radiofreq%FC%EAncia-Apresenta%E7%E3o
[5] Brasil 247 – O crescente risco da poluição eletrônica – http://www.brasil247.com/pt/247/revista_oasis/82535/
[6] IEAv – Instituto de Estudos Avançados – Departamento de Ciência e Tencnologia Aeroespacial – Análise de ambientes eletromagnéticos em laboratórios da área de RF – p.83 – http://www.ieav.cta.br/wai8/pdf/Caderno_Institucional.pdf
[7] Ecologia Médica – Você é alérgico à internet sem fio? – http://www.ecologiamedica.net/2013/02/eletrosmog-voce-e-alergico-internet-sem.html
[8] Sítio francês dedicado à poluição eletromagnética – http://www.electrosmog.info/
[9] Bertrik – Testes em 433 Mhz – http://bertrik.sikken.nl/433mhz/index.html
[10] Julio Battisti – Radiofrequência, fundamentos – http://www.juliobattisti.com.br/tutoriais/paulocfarias/redeswireless003.asp
[11] CINEL – Manual de Antenas, Propagação e Linhas de Transmissão – http://opac.iefp.pt:8080/images/winlibimg.exe?key=&doc=73187&img=1182
[12] RFM – Antenas para aplicações de baixa potência – http://www.rfm.com/corp/appdata/antenna.pdf
[13] Datasheet Catalog – Folhas de dados do UM3750 – http://www.datasheetcatalog.org/datasheets/150/367002_DS.pdf
[14] Farnell – Folhas de dados do National MM53200 – http://www.farnell.com/datasheets/105708.pdf
[15] Holtek – Folhas de dados dos circuitos integrados HT12E e HT12D – http://www.holtek.com.tw/english/products/
[16] Princeton – Folhas de dados dos CI’s PT2260, PT2262 e PT2264 e respectivos pares – http://www.princeton.com.tw/en-us/products/encoderdecodericseries/fixedcodeencoderic.aspx
[17] Freescale – Folhas de dados do par codificador/decodificador MC145026P e MC145027P – http://www.freescale.com/files/rf_if/doc/data_sheet/MC145026.pdf
[18] Rentron – Folhas de dados do CIP-8, codificador/decodificador de 8 bit – http://www.rentron.com/Files/CIP8_TWS8BIT.pdf – http://www.rentron.com/Files/CIP-8.pdf
[19] Holtek – Características do HT6P20B – http://www.holtek.com.tw/english/docum/consumer/6p20x2.htm
[20] Testes com PT2262 para Arduino – http://dzrmo.wordpress.com/2012/07/08/remote-control-pt2272-for-android/
[21] Cintron – Remote Control 315 Mhz – tutorial – http://tutorial.cytron.com.my/2012/09/03/remote-control-315mhz/
[22] Como montar um circuito de controle remoto com microcontrolador Atmel – http://www.serasidis.gr/circuits/RF_remote_control/RF_remote_control.htm
[23] Futura Elettronica – Circuito de controle remoto de longa distância UHF – 400 mW – http://www.futuraelettronica.net/pdf_ita/7100-FT151K.pdf
[24] Nutchip – Controle remoto 6 canais – http://www.nutchip.com/progetti/picrmt/picrmt-6-rf_en.htm
[25] Blog Homemade Circuits Just for You – Circuito de controle remoto RF com HT12 – http://homemadecircuitsandschematics.blogspot.com.br/2011/12/make-hi-end-rf-remote-control-circuit.html
[26] Rentron – Circuitos de controle remoto 433 MHz – http://www.rentron.com/rf_remote_control.htm
[27] Rentron – Circuito de controle remoto com o par R-8PD e R-8PE – http://www.rentron.com/remote_control/8P-ENC_DEC.PDF
[28] Schema-electronique – Circuito de controle remoto 433 Mhz com integrado Micrel MICRF001BN – Em francês, usar o tradutor do site – http://www.schema-electronique.net/2010/07/un-recepteur-de-telecommande-uhf.html
[29] Schema-electronique – Circuito de controle remoto com 4 canais, 433MHz com UM86409 – Em francês, usar o tradutor do site – http://www.schema-electronique.net/2012/02/une-radiocommande-sortie-analogique.html
[30] Omron – Datasheet das chaves tact B3F – http://www.omron.com/ecb/products/pdf/en-b3f.pdf – http://industrial.omron.com.br/uploads/arquivos/D22B3F0305.pdf
[31] Norma RoHS – definições de percentuais – http://www.rohscompliancedefinition.com/
[32] RoHS Brasil – prazo de aplicação da norma – http://www.intertek-cb.com/brazil/portuguese/rohsbrasil.shtml
[33] WD-40 – Vídeos explicativos com os usos do WD-40 – http://www.wd40.com.br/
ep/
Comments